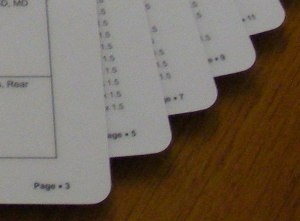
The clear plastic film used to laminate printing is available in a variety of thicknesses. The thicker the laminate used, the more rigid the finished piece becomes. And as the piece becomes more rigid, a sharp 90-degree corner is more likely to cause a skin puncture or other injury.
That is why we always recommend rounding the corners of laminated pieces if they will pose a hazard during handling. For example, printed pieces covered with a laminate of 5 mil or thicker should always have its corners rounded. This applies whether the finished piece has a sealed edge or is flush cut.
Thinner laminates, such as 1.5 or 3 mil, can also pose a danger. This is particularly true if the finished piece is flush cut instead of having a sealed edge, or if the laminate is applied over a thick paper substrate. In these instances, the resulting rigidity of the corners should be weighed against the frequency of handling to determine if rounded corners are necessary.
As a rule of thumb, the corners can generally remain square (un-rounded) if the finished piece is thin enough to remain pliable at its edge. However, if the laminated pieces will be handled by children, such as flash cards or other educational materials, it is a good practice to round the corners regardless of the thickness. When young kids are involved, it is always better to err on the side of caution.
In addition to softening sharp edges for safety reasons, corner rounding also adds a more finished and professional look to laminated printing. If you have a lamination project coming up in the near future, give Formax Printing Solutions a call at 866.367.6221 or submit our quote request form. We have great pricing on printing and laminating!
Take care! Rick