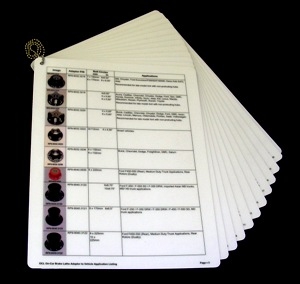
What is Laminated Printing and How Does It Work?
Laminated Printing refers to printed pieces that have been enclosed between two sheets of clear plastic film.
Printing is laminated to protect it from stains and moisture, to increase its strength and durability, and to add sheen and vibrancy to its ink colors.
If you have an upcoming print project that will require lamination, below are five important things to consider. These five questions will help you select the type of lamination that best corresponds to your specific needs.
1) What Thickness Fits Your Project?
Laminate film comes in a variety of thicknesses, which are measured in mils. One mil is equal to .001" or 1/1000ths of an inch. Thus, laminate film measuring 1.5 mil would be .0015" thick and laminate film measuring 10 mil would be .010" thick.
Because your printing will be sandwiched between two pieces of laminate, a 1.5 mil laminate will increase the overall thickness of your printed piece by 3 mil (.003"). Likewise, a 10 mil laminate will increase the overall thickness by 20 mil (.020").
Basically, the more rigid you would like your finished printed piece to be, the thicker the laminate you would choose. However, if your printed piece is to be folded, it is usually best to use a laminate film thickness of 3 mil or less. As you would expect, folding becomes more difficult as the laminate thickness increases.
2) Do You Prefer a Gloss or Matte Finish?
Laminate film comes in several sheen levels. The sheen level you select will depend upon the type of project as well as your personal preference.
Glossy laminate films add a shiny, glass-like appearance to printed materials. A gloss laminate also greatly enhances the color and vibrancy of the underlying ink. This makes it a popular choice for promotional pieces - like presentation folders and showroom displays - and for the covers of bound information - such as books, reports and training materials.
A matte laminate gives a somewhat softer appearance to printed pieces and helps reduce glare. Because of its reduced sheen level, matte lamination allows for easier reading of printed information. This makes it a good choice for restaurant and bar menus, maps, and the pages of books, manuals and binders.
3) Sealed Edge or Flush Edge?
A sealed edge refers to lamination that extends beyond the edge of the printed piece. A flush edge refers to lamination that is trimmed even with the edge of the printed piece.
A sealed edge is often used if the print matter is to be used in an environment where moisture, oil, grease or other contaminants may be present. In cases like these, the lamination film is extended beyond the edge of the printed piece by 1/8" to 1/2" so that the top and bottom sheets of laminate bond to each other around the perimeter of the printed piece. This ensures fluids and dirt never contact the edge of the printed paper substrate.
A flush edge is used for printed pieces that will not be subject to moisture or excessive dirt- or whenever the desired aesthetics warrant a flush edge. For example, a flush edge is commonly used for business cards or the interior pages of a book or binder.
4) Should the Corners be Square or Rounded?
Depending on the thickness of the laminate film used, a printed piece can become quite rigid. And when this happens, a 90 degree corner can become rather sharp. If the piece is something that will be handled frequently, especially by children, it is wise to shape the corner so that it doesn't become a safety concern.
The most common way to make the corners of rigid pieces more user-friendly is to round them off. In addition to being safer, rounded corners add a nice finished look.
In our experience, the corners can remain square (un-rounded) if the laminate is thin enough to remain pliable.
5) Are There Any Additional Finishing Operations?
After being printed and laminated, it is not uncommon for laminated printing to receive some form of supplementary operation.
For example, inserts going into a ringed binder may require drilling (hole punching) along one edge. Similarly, laminated tags and operating instructions are often designed to hang from merchandise or machinery via a hook or tie. These will need one or more holes near an edge or corner, sometimes with an eyelet installed in the hole(s).
Also, laminated printing is sometimes die-cut into a special shape, such as the tabbed dividers used in a custom binder or a creatively-designed bookmark. A laminated piece may also require scoring and folding, such as for a menu. In addition, laminated printing is used to create erasable memo boards, which almost always requires the installation of magnets or an adhesive medium to the back.
If you have any additional questions about laminated printing, just give Formax a call at 866-367-6221. We can assist you with short or long production runs. Plus, we can give you some money-saving ideas too!
Take care! Rick