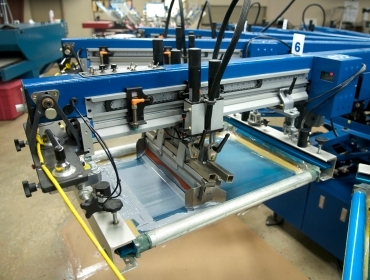
A commercial screen printing press. Shown as its automated arm squeegees ink through a woven screen.
Screen Printing is a time-tested stenciling technique used to apply inked images to a wide variety of substrates. Using a stencil, or a series of stencils, the ink is distributed to the desired area(s) by being pressed through a porous screen, hence the name Screen Printing.
Also known as silkscreen, serigraphy, or serigraph printing, Screen Printing can be performed as a manual or automated process.
How Does the Screen Printing Process Work?
At the core of the screen printing process is a mesh screen material that has been stretched tightly across a rigid frame. Though silk mesh was used at one time, modern mesh is often woven from polyester or stainless steel threads.
The areas of the finished design that will not receive ink coverage are masked out on the screen using a stencil. These masked sections will block ink from passing through the screen. The unmasked sections will allow ink to pass through, thus transferring the intended image onto the substrate to be printed.
Once the screen assembly is placed over the substrate, a squeegee is used to press moderately thick ink through the screen mesh. The squeegee blade, which is usually made of synthetic rubber or polyurethane, must be firm yet flexible in order to evenly disperse the ink.
As the squeegee moves across the screen, the mesh and its corresponding stencil regulate the placement of the ink onto the substrate. The thread count and the diameter of the threads in the mesh are other factors that determine how defined the final image will be.
With screen printing, colors are applied one at a time. If the printed design has multiple colors, the process is repeated using different stenciled screens and ink colors. Thus, each layer of ink color helps to create the final design. In order to produce the highest quality image, each screen used for the design must be in perfect alignment so that each color is properly placed.
Screen Printing is Versatile, Durable, and Vibrant
One of the main advantages of screen printing is its versatility. While offset and digital printing methods are still the best choices for high-resolution printing on paper, screen printing opens up a whole new world of substrate options. In fact, the screen printing process can apply long-lasting images to virtually any printable surface, including fabric, vinyl, rigid plastic, foam board, metal, glass and many others.
Another major advantage of screen printing is its durability. Compared to other printing methods, the screen printing process can apply very heavy ink coverage, resulting in a longer-lasting design. Also, depending on the project, certain coatings and additives can be used to make the ink resistant to UV rays, moisture, scratches, and/or chemicals. This allows screen printed products to be used outdoors and in other harsh environments for years without fading.
A third advantage of screen printing is the vibrancy of the ink colors. The greater ink thickness achieved with the screen printing method means more color pigments are applied to the substrate. The more pigments, the bolder and brighter the colors. In addition, many screen-printed projects use PMS or "spot" colors. For multi-colored designs, these spot colors are applied as separate layers, allowing each color to maintain its true brilliancy.
Even though Formax doesn't offer every type of screen-printed product (like T-shirts), below is a list of the flat sheet products we can assist you with-
- Indoor and Outdoor Banners
- Yard Signs
- Posters
- Decals, Labels and Nameplates
- Domed and Embossed Decals
- Static Clings
- Bumper Stickers
- Vehicle Mirror Hangers
- Hang Tags and Door Hangers
- Point of Purchase (POP) Signs
If you have an upcoming project that requires Screen Printing, give Formax Printing Solutions a call at 866-367-6221. Or, if you already know the specs of your project, simply click here to access our quote request form. We look forward to serving your screen-printing needs.
Take care! Rick